Select your machine to go to the FAQ
1 LOKLiK IdeaStudio™
1.1 Download and install LOKLiK IdeaStudio™ & APP
1.2 What is "Standard Cut"?
Standard Cut mode is a conventional cutting format that includes clearly defined cut lines. This mode supports a wide range of designs, from simple single-line cuts to more complex segmented cuts that can be assembled or layered with different materials or colors.
In LOKLiK IdeaStudio™, designs in Standard Cut mode may appear as basic red cut lines, regardless of whether they contain color in the original file.
This mode is commonly used for cutting materials such as vinyl, heat transfer paper, fabric, and similar project.
1.3 What is "Print Then Cut"?
Print Then Cut mode allows you to print your design using a home printer and then precisely cut it with your Loklik iCraft™.
In LOKLiK IdeaStudio™, registration marks are automatically added to ensure accurate alignment during the cutting process.
This mode is ideal for projects such as printable vinyl, stickers, temporary tattoos, and other similar materials.
1.4 What are the differences between "Standard Cut" and "Print Then Cut"?
-
Print Then Cut Mode requires turning on registration marks to ensure precise cutting alignment after printing. This mode is used for printable materials such as stickers, printable vinyl, and other designs that involve detailed colors and intricate patterns. A printer is necessary for this process.
-
Standard Cut Mode does not require registration marks and relies on specific cut lines. The color in your final design comes from the material itself rather than being printed. This mode is ideal for materials like cardstock, textured vinyl, and heat transfer vinyl, which do not require additional printing.
When using Standard Cut Mode, avoid enabling registration marks, even if your design includes colors, as the device will attempt to locate them before cutting.
1.5 Can I work offline with LOKLiK IdeaStudio™?
Yes, LOKLiK IdeaStudio™ supports offline operation.
Even if your network disconnects on your computer, you can still continue the cutting process without any interruptions.
1.6 Can I continue the current cutting process if the network disconnects?
Yes, LOKLiK IdeaStudio™ supports offline operation.
Even if your network disconnects on your computer, you can still continue the cutting process without any interruptions.
1.7 How do I set the canvas unit in LOKLiK IdeaStudio™?
- Click on the Account Menu and select Settings.
- Choose your preferred unit (inches or millimeters) and apply the change.
1.8 How can I restore designs or folders deleted from "My Zone"?
You can find and restore deleted designs or folders in the Trash Bin within LOKLiK IdeaStudio™.
1.9 How to set up cutting parameters?
1.10 How do I change the language in LOKLiK IdeaStudio™?
- Click on the Account Menu and select Settings.
- Click on Language to switch to your preferred language.
LOKLiK IdeaStudio™ supports multiple languages, including Chinese, English, German, Spanish, French, Italian, Dutch, Portuguese and more.
We are continuously expanding our language options to enhance user experience worldwide.
1.11 Can't find your answer?
2 LOKLiK iCraft™
2.1 Where can I download the manual?
2.2 How to properly calibrate your Loklik iCraft™ for optimal performance
1. Ensure your Loklik iCraft™ is up to date
Make sure your Loklik iCraft™ is running the latest firmware version.
Follow the update instructions for your device:
2. Calibration process
Your Loklik iCraft™ may require multiple calibrations due to offset adjustments. If repeated calibrations are unsuccessful, try resetting the calibration values before recalibrating.
3. Recommended ppaper size for calibration
For the best calibration accuracy, use the same paper size for both calibration and Print-then-Cut operations. Recommended sizes:
- A4 (21.0 × 29.7 cm / 8.27 × 11.69 in)
- Letter (21.59 × 27.94 cm / 8.50 × 11.00 in)
2.3 Which blade should I use for Loklik iCraft™?
Choosing the right blade for your material ensures optimal cutting results:
Fine-Point Blade (Delivered with iCraft)
- Best for lightweight to medium-weight materials
- Ideal for paper, vinyl, stickers, cardstock, and similar materials
Deep-Point Blade (Optional)
- Designed for thicker materials up to 2 mm
- Suitable for leather, thick cardboard, and other dense materials
2.4 Unable to cut through the material on Loklik iCraft™
1. Verify material selection in Loklik IdeaStudio™ or the app
Ensure you are cutting the exact material selected in your settings for optimal results.
2. Check the blade and blade housing
- Remove any residues from the blade and blade housing.
- Ensure the blade housing is installed correctly and firmly.
3. Secure the material on the mat
- Make sure the material is flat and properly secured to the mat to prevent shifting.
- It is recommended to use materials thinner than 2 mm for best cutting performance.
4. Adjust cutting force
- Calibrate the cutting force in Loklik IdeaStudio™:
Go to Device > Device Calibration and adjust the settings.
- Increase the cutting force if necessary.
- If the material is not cut through at maximum pressure, try cutting multiple times.
5. Check blade condition
- If the blade has been used for a long time, it may have dulled—replace it with a new one.
- Ensure the blade is properly fastened and that the blade housing is functioning correctly.
- If the blade housing is damaged, consider replacing it.
2.5 Loklik iCraft™ is cutting too deep
1. Verify material selection in Loklik IdeaStudio™ (pc or app)
Make sure you have selected the correct material in your settings to ensure precise cutting.
2. Adjust cutting force
- Try lowering the cutting force to prevent overcutting.
- Calibrate the cutting force in Loklik IdeaStudio™ :
Go to Device > Device Calibration and adjust the settings accordingly.
2.6 Unable to calibrate cutting force on Loklik iCraft™
If you're having trouble calibrating the cutting force, follow these steps:
1. Update your Loklik iCraft™ firmware
Ensure your Loklik iCraft™ is running the latest firmware for optimal performance.
Follow the update guide for your device:
2. Reset and recalibrate
Before calibrating again, reset the calibration settings:
- Go to IdeaStudio > Device > Reset Calibration Value
- After resetting, attempt the calibration process again.
Keeping your firmware updated and properly resetting calibration can help ensure accurate cutting force adjustments. If the issue persists, try increasing or decreasing the cutting force manually based on your material.
2.7 Why isn't my material sticking firmly to the cutting mat?
Ensure you're using the correct mat for your material, and make sure the mat is clean.
If necessary, replace it with a new cutting mat for better adhesion.
Here you can find the recommended material for each mat:
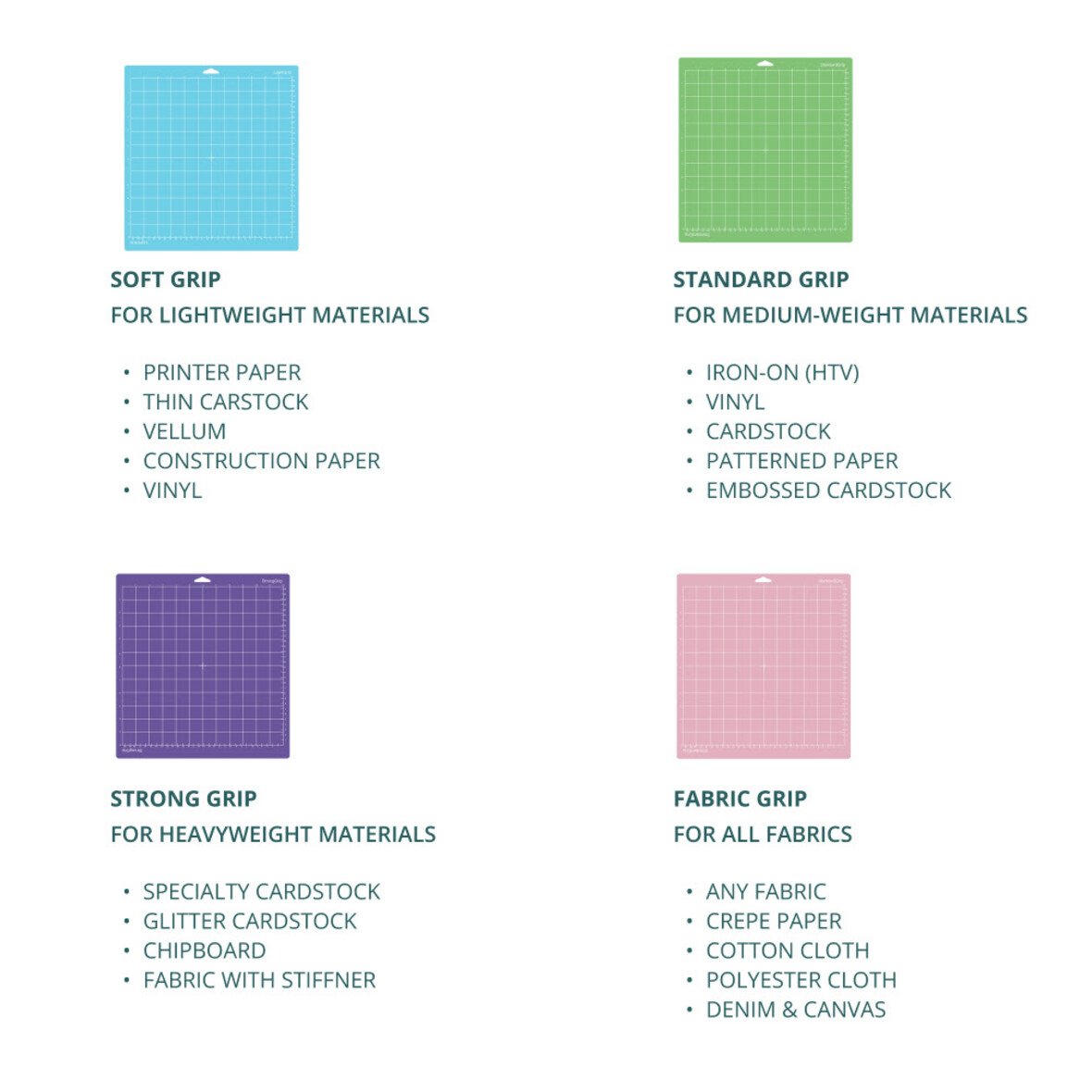
2.8 Materials are curling when cutting
If your materials are curling during cutting, try the following solutions:
1. Check the cutting mat
- Remove the protective film from the cutting mat before use.
- Ensure the material is firmly adhered to the mat.
- If the mat has lost its stickiness, replace it for better grip.
2. Proper mat placement
- Follow the setup instructions carefully.
- Ensure the cutting mat is correctly positioned in the mat slots on the iCraft to avoid shifting during cutting.
2.9 The material is torn or distorted when cutting
- Ensure you're cutting the correct material selected in the software.
- Check that your design isn't too small or complex. We recommend cutting a larger or simpler design.
- Clear any residues from the blade and blade housing.
- Incompatible materials may cause this issue. Test different materials with the same settings to see if the problem persists, or adjust the settings for your material.
- Lower the cutting speed to prevent distortion.
- If the blade has become dull from long-term use, replace it with a new one.
- Make sure the blade is securely fastened and the blade housing is functional. If needed, fasten the blade or replace the blade housing.
- Replace the cutting mat and try cutting again.
2.10 How to achieve a successful cutting result with Loklik iCraft™?
To ensure precise and clean cuts, follow these steps:
1. Use the correct blade
- Ensure you have installed the right blade for your material (Fine-Point or Deep-Point blade).
2. Set up material & parameters properly
- Select the correct material settings in your LOKLiK IdeaStudio™.
- Adjust the cutting force and speed according to the material.
3. Check blade housing installation
- Make sure the blade housing is correctly installed and secured.
4. Ensure the material is properly placed
- The material should be flat and firmly secured on the cutting mat.
- If using Heat Transfer Vinyl (HTV) or Permanent Vinyl, ensure the cutting side is facing up.
5. Follow material thickness guidelines
- It is recommended to use materials thinner than 2 mm for best results.
6. Calibrate the cutting force
- If issues persist, calibrate the cutting force in LOKLIK IdeaStudio™:
Go to Device > Device Calibration and make the necessary adjustments.
2.11 How to achieve a successful print-then-cut result with Loklik iCraft™?
To ensure your print-then-cut process goes smoothly, follow these steps:
1. Proper placement in your printer
- Ensure the material is correctly placed in the printer tray when printing.
2. Clear registration marks
- After printing, make sure the registration marks are clear and visible for accurate scanning.
Check that the registration marks are clear and visible. If needed, darken the marks with a black pen for better contrast.
3. Align material on the cutting mat
- Align and stick the material on the left top corner of the cutting mat for precise positioning.
- Ensure the material is flat and firmly secured to avoid shifting during cutting.
4. Load the mat gently
- Hold the cutting mat gently by hand when loading the materials into the Loklik iCraft™.
- When loading the material, ensure the silicone rings aligns with the registration marks on the material for accurate scanning.
5. Calibrate the print-then-cut function
- If needed, calibrate the print-then-cut function in LOKLiK IdeaStudio™:
Go to Device > Device Calibration and complete the calibration process.
2.12 What to do if the print-then-cut function performs poorly on Loklik iCraft™?
If you're experiencing issues with the print-then-cut function, try the following solutions:
1. Calibrate the print-then-cut function
- Start by calibrating the print-then-cut function in LOKLIK IdeaStudio™:
Go to Device > Device Calibration and follow the steps to recalibrate.
2. Check registration marks alignment
- When loading the material, ensure the silicone rings aligns with the registration marks on the material for accurate scanning.
3. Clean the cutting mat
- Clean the cutting mat to ensure it's free of dust or debris that could affect the cutting process.
4. Ensure material is flat and secured
- Make sure the material on the mat is flat and firmly secured to prevent any shifting during the cut.
5. Align the cutting mat properly
- When loading materials, align the edge of the cutting mat closely to the slots to ensure proper feeding into the Loklik iCraft™.
2.13 What should I do if I can't find my material's cutting parameter in the software?
Try using the cutting parameter for a similar material (recommended cutting thickness: <2 mm).
We recommend performing a test cut to ensure the settings work properly for your material.
If needed, you can customize the cutting parameter for a more accurate result.
2.14 Why are there abnormal sounds during cutting?
If you hear abnormal sounds during the first operation please check the following:
- Check and clear any residues or scraps around the blade housing, then try cutting again.
- Ensure you're using the original power adapter to avoid incorrect voltage input.
- Make sure the device is placed on a stable and flat surface while operating.
If these didn't solve the issue, please record a video and contact us for assistance.
2.15 Can I use smart/matless materials from other brands then LOKLiK?
Yes, the Loklik iCraft™ supports infinite cutting with smart/matless materials from other brands as well.
Please note:
- Try using the cutting parameter for a similar material (recommended cutting thickness: <2 mm).
- We recommend performing a test cut to ensure the settings work properly for your material.
- If needed, you can customize the cutting parameter for a more accurate result.
2.16 I cannot connect the Loklik iCraft™ via Bluetooth
- Ensure the device is powered on.
- Make sure the device is not connected via USB (unplug the cable if needed).
- Check for other Bluetooth devices nearby and turn them off before trying again.
- Ensure the device is close enough to your computer or mobile device and reduce the distance if needed.
Check this link for more information.
2.17 What should I do if I fail or am unable to update the firmware in LOKLiK IdeaStudio™ or theLOKLiK IdeaStudio™ app?
Please visit this link to download the flashtool and follow the steps outlined in the manual.
2.18 What should I do if my Loklik iCraft™ doesn't power on anymore?
- First, ensure the device is properly powered on. Check that it's plugged in and the power cable and source is functional.
- Press the "Power" button briefly (a short press) to turn the device on. If it doesn’t respond, try pressing it again.
- If the device still doesn't turn on, it may need a firmware update. Open LOKLiK IdeaStudio™ and update the device to the latest firmware version. This can resolve potential software-related issues.
- If you're still experiencing issues, we recommend downloading the flashtool to perform a manual update. Visit this link to download the flashtool and carefully follow the steps outlined in the manual.
If these didn't solve the issue, contact us for assistance.
2.19 My Loklik iCraft™ fails to read the registration marks. What should I do?
- Ensure the material is properly aligned to the top-left corner of the cutting mat, and use a LOKLiK scrapper squeegee or roller to make sure the material is fully flat on the cutting mat.
- Check that the registration marks are clear and visible. If needed, darken the marks with a black pen for better contrast.
- Make sure your print settings are set to Actual Size (100% scale), Borderless Printing, or Fit to Page Margins to avoid any scaling issues.
- Verify that the paper is placed correctly in your printer tray to prevent skewed registration marks.
- Avoid using glossy paper, as its surface may interfere with mark detection; matte paper is recommended for better results.
- Ensure the mat is firmly attached to the device roller before loading. Gently hold the mat’s ends during the loading process to prevent misalignment.
- Check that the mat is not bent or creased, as this can lead to poor cutting results or unreadable registration marks. Adjust the mat if needed.
- Ensure your firmware is up-to-date. For guidance, refer to these links on how to update the iCraft™:
2.20 Can't find your answer?
3 LOKLiK Crafter
3.1 Where can I download the manual?
3.2 Crafter doesn't cut in the right place
Please calibrate the Print-then-Cut function in LOKLiK IdeaStudio™ for the Crafter*.
This can be done in:
- IdeaStudio > Device > Device Calibration
*Crafter is the older version so not the same as the LOKLiK iCraft™
3.3 I can't get the Print-then-Cut function calibrated correctly
Before starting: make sure that your Crafter is updated to the latest firmware version:
Go to LOKLiK IdeaStudio™:
- IdeaStudio > Device > Device Calibration
Multiple calibrations may be needed based on the device's offset.
If multiple calibrations are unsuccessful, please try to reset calibration value and recalibrate.
To ensure optimal calibration quality, it is recommended to use the same paper size for both calibration and "Print-then-Cut" operations.
Suggested paper sizes:A4 (21.0 x 29.7 cm / 8.27 x 11.69 in) | Letter (21.59 x 27.94 cm / 8.50 x 11.00 in);
3.4 I cannot cut through the material
1. Verify material selection in Loklik IdeaStudio™ or the app
Ensure you are cutting the exact material selected in your settings for optimal results.
2. Check the blade and blade housing
- Remove any residues from the blade and blade housing.
- Ensure the blade housing is installed correctly and firmly.
3. Secure the material on the mat
- Make sure the material is flat and properly secured to the mat to prevent shifting.
- It is recommended to use materials thinner than 2 mm for best cutting performance.
4. Adjust cutting force
- Calibrate the cutting force in Loklik IdeaStudio™:
Go to Device > Device Calibration and adjust the settings.
- Increase the cutting force if necessary.
- If the material is not cut through at maximum pressure, try cutting multiple times.
5. Check blade condition
- If the blade has been used for a long time, it may have dulled—replace it with a new one.
- Ensure the blade is properly fastened and that the blade housing is functioning correctly.
- If the blade housing is damaged, consider replacing it.
3.5 My Crafter is cutting too deep
1. Verify material selection in Loklik IdeaStudio™ (pc or app)
Make sure you have selected the correct material in your settings to ensure precise cutting.
2. Adjust cutting force
- Try lowering the cutting force to prevent overcutting.
- Calibrate the cutting force in Loklik IdeaStudio™ :
Go to Device > Device Calibration and adjust the settings accordingly.
3.6 I can't get the cutting force calibrated correctly
If you're having trouble calibrating the cutting force, follow these steps:
1. Update your LOKLiK Crafter firmware
Ensure your Loklik iCraft™ is running the latest firmware for optimal performance.
Follow the update guide for your device:
2. Reset and recalibrate
Before calibrating again, reset the calibration settings:
- Go to IdeaStudio > Device > Reset Calibration Value
- After resetting, attempt the calibration process again.
Keeping your firmware updated and properly resetting calibration can help ensure accurate cutting force adjustments. If the issue persists, try increasing or decreasing the cutting force manually based on your material.
3.7 Which blade should I use on my Crafter?
Choosing the right blade for your material ensures optimal cutting results:
LOKLiK Cutting Blade 45°(red cover)
- Best for lightweight to medium-weight materials
- Ideal for paper, vinyl, stickers, cardstock, and similar materials
LOKLiK Cutting Blade 60°(blue cover)
- Designed for thicker materials up to 1.5 mm
- Suitable for craft foam, chipboard, glitter cardstock, aluminum foil, cardboard, matboard, poster boards and other dense materials
3.8 Materials are curling when cutting
If your materials are curling during cutting, try the following solutions:
1. Check the cutting mat
- Remove the protective film from the cutting mat before use.
- Ensure the material is firmly adhered to the mat.
- If the mat has lost its stickiness, replace it for better grip.
2. Proper mat placement
- Follow the setup instructions carefully.
- Ensure the cutting mat is correctly positioned in the mat slots on the iCraft to avoid shifting during cutting.
3.9 The material is torn or distorted when cutting
- Ensure you're cutting the correct material selected in the software.
- Check that your design isn't too small or complex. We recommend cutting a larger or simpler design.
- Clear any residues from the blade and blade housing.
- Incompatible materials may cause this issue. Test different materials with the same settings to see if the problem persists, or adjust the settings for your material.
- Lower the cutting speed to prevent distortion.
- If the blade has become dull from long-term use, replace it with a new one.
- Make sure the blade is securely fastened and the blade housing is functional. If needed, fasten the blade or replace the blade housing.
- Replace the cutting mat and try cutting again.
3.10 Why are there abnormal sounds during cutting?
If you hear abnormal sounds during the first operation please check the following:
- Check and clear any residues or scraps around the blade housing, then try cutting again.
- Ensure you're using the original power adapter to avoid incorrect voltage input.
- Make sure the device is placed on a stable and flat surface while operating.
If these didn't solve the issue, please record a video and contact us for assistance.
3.11 I cannot connect the Loklik Crafter via Bluetooth
- Ensure the device is powered on.
- Make sure the device is not connected via USB (unplug the cable if needed).
- Check for other Bluetooth devices nearby and turn them off before trying again.
- Ensure the device is close enough to your computer or mobile device and reduce the distance if needed.
Check this link for more information.
3.12 What should I do if I fail or am unable to update the firmware in LOKLiK IdeaStudio™ or the LOKLiK IdeaStudio™ app?
Please visit this link to download the flashtool and follow the steps outlined in the manual.
3.13 Why doesn't the Crafter stop cutting immediately when pressing the "Pause" button?
There is usually a short delay when pausing the process because the device needs time to process the next cutting command before stopping.
3.14 What to do if my LOKLiK Crafter doesn't power on anymore?
Please visit this link to download the flashtool and follow the steps outlined in the manual.
3.15 My Crafter fails to read the registration marks.
- Ensure the material is properly aligned to the top-left corner of the cutting mat, and use a LOKLiK scrapper squeegee or roller to make sure the material is fully flat on the cutting mat.
- Check that the registration marks are clear and visible. If needed, darken the marks with a black pen for better contrast.
- Make sure your print settings are set to Actual Size (100% scale), Borderless Printing, or Fit to Page Margins to avoid any scaling issues.
- Verify that the paper is placed correctly in your printer tray to prevent skewed registration marks.
- Avoid using glossy paper, as its surface may interfere with mark detection; matte paper is recommended for better results.
- Ensure the mat is firmly attached to the device roller before loading. Gently hold the mat’s ends during the loading process to prevent misalignment.
- Check that the mat is not bent or creased, as this can lead to poor cutting results or unreadable registration marks. Adjust the mat if needed.
- Ensure your firmware is up-to-date. For guidance, refer to these links on how to update the Crafter:
3.16 Can't find your answer?
4 LOKLiK ImPress™ Auto 2-Smart
4.1 Where can I download the manual?
4.2 Why does the device emit slight smoke during or after heating?
It is normal for slight smoke to be emitted, as the sublimation ink sublimates into gas at high temperatures. This is a standard part of the sublimation process and should not be a cause for concern.
4.3 What is the time and temperature range of the LOKLiK ImPress™ Auto 2-Smart?
- Time Range: 1 - 199 seconds
- Temperature Range: 100°C - 210°C (210°F - 410°F)
4.4 How do I set the temperature unit (°C or °F) or Pressure unit (kg/lb)?
Go on your LOKLiK ImPress™ Auto 2-Smart to > System > Units.
Select the units of your choice:
- Temperature units: ℃ (Celsius) or ℉ (Fahrenheit)
- Pressure unit: kg (Kilogram) or lb (Pound)
4.5 What to do if I cannot find my materials or substrates in the "Material Library"?
Try selecting similar materials or substrates from the "Material Library." If needed, you can customize the ironing parameters for your specific materials or substrates.
4.6 Why have my customized settings been cleared?
Customized settings are cleared when the machine is restored to its default settings.
4.7 How to get a successful heat transfer result?
- Make sure you have followed the instructions correctly.
- Ensure you have selected the correct materials and substrates.
- For fabrics, iron them first to remove wrinkles before heat transferring.
- It is recommended to use LOKLiK's materials for the best ironing results.
4.8 Why is my machine making beep sounds?
- Beep once: the machine is powered, turned on/off, finishes time/temp/pressure setting, or the countdown ends.
- Beep constantly: the heat plate is pressing down.
- Beep constantly with "E1/2/3/4/5" on the screen: cut the power immediately and restart the machine after letting it cool down.
4.9 What to do if the screen cannot descend/ascend accordingly?
- Cut off the power, re-power the machine, and restart the machine.
- Do NOT move the touch screen manually, as it may cause malfunction.
- Contact LOKLIK's customer service if the above steps don't work.
4.10 What size and thickness can the LOKLiK ImPress™ Auto 2-Smart press?
The heat plate has a size of 38 x 38 cm and can press materials up to 4.5 cm thick.
4.11 Can the LOKLiK ImPress™ Auto 2-Smart be used for DTF?
Yes, thanks to the increased pressure, the LOKLiK ImPress™ Auto 2-Smart is well-suited for DTF (Direct to Film) transfers.
4.12 How much pressure can the LOKLiK ImPress™ Auto 2-Smart generate?
The LOKLiK ImPress™ Auto 2-Smart can generate a pressure range of 20 - 80 kg.
4.13 What materials can be used to press with the LOKLiK ImPress™ Auto 2-Smart?
The LOKLiK ImPress™ Auto 2-Smart can work with a variety of materials, including:
If you're not sure if your material can be used, we recommend checking with the supplier to make sure it's safe.
4.14 What materials can the LOKLiK ImPress™ Auto 2-Smart press on?
The LOKLiK ImPress™ Auto 2-Smart is compatible with a variety of materials, including:
- Cotton
- Polyester
- Blends (Cotton-poly, etc.)
- And other fabrics, depending on the material and technique used for pressing.
Some third-party materials may work better than others, and the results can vary. We recommend contacting your supplier to confirm if it's compatible with our easy heat press and testing different settings to achieve the desired results.
4.15 Can't find your answer?
5 LOKLiK Auto Heat Press
5.1 Where can I download the manual?
5.2 Why does the device emit slight smoke during or after heating?
It is normal for slight smoke to be emitted, as the sublimation ink sublimates into gas at high temperatures. This is a standard part of the sublimation process and should not be a cause for concern.
5.3 What is the time and temperature range of the LOKLiK Auto Heat Press?
- Time Range: 1 - 199 seconds
- Temperature Range: 100°C - 210°C (210°F - 410°F)
5.4 How do I set the temperature unit (°C or °F) ?
Press the "Temp" button for 2 seconds to switch between temperature units (℃/℉).
5.5 Why do I see vague white spots in my transfer results?
This issue is often caused by insufficient heat or pressing time.
To achieve the best results, follow these steps:
- Check the correct settings in the LOKLiK Auto Heat Press manual and ensure they are applied correctly.
- White spots usually indicate that not enough time or heat was used during pressing.
Try increasing the temperature or pressing time.
- Make sure the materials are positioned completely flat. The harder side of the mat should be facing up.
- If the heat mat is warped or no longer flat, replace it to ensure even pressure distribution.
- Some third-party materials may work better than others, and the results can vary. We recommend contacting your supplier to confirm if it's compatible with our Auto Heat Press and testing different settings to achieve the desired results.
5.6 Why are my image colors uneven or dull after pressing?
Uneven or dull colors are usually caused by insufficient heat or pressing time. Follow these steps to improve your results:
- Refer to the LOKLiK Auto Heat Press manual to ensure you are using the correct settings.
- Make sure the materials are positioned flat and secure before pressing.
- The harder side of the mat should be facing up for an even transfer.
- If the mat is no longer flat, consider replacing it for better results.
5.7 Can I use the LOKLiK Auto Heat Press for DTF?
We do not guarantee optimal results when using the LOKLiK Auto Heat Press for DTF (Direct to Film) transfers. The pressure generated by the machine may not be high enough for a successful transfer.
We recommend to using our LOKLiK ImPress™ Auto 2-Smart for DTF (Direct to Film) transfers.
5.8 What materials can be used with the LOKLiK Auto Heat Press?
The LOKLiK Auto Heat Press can work with a variety of materials, including:
If you're not sure if your material can be used, we recommend checking with the supplier to make sure it's safe.
5.9 What materials can the LOKLiK Auto Heat Press press on?
The LOKLiK Auto Heat Press is compatible with a variety of materials, including:
- Cotton
- Polyester
- Blends (Cotton-poly, etc.)
- And other fabrics, depending on the material and technique used for pressing.
Some third-party materials may work better than others, and the results can vary. We recommend contacting your supplier to confirm if it's compatible with our easy heat press and testing different settings to achieve the desired results.
5.10 What size and thickness can the LOKLiK Auto Heat Press handle?
The LOKLiK Auto Heat Press features a:
5.11 Why does the error "E1" or "E2" appear on the screen?
- E1 with beep: This error occurs when the temperature hasn’t risen within 30 seconds during heating.
- E2 with beep: This error occurs when the temperature exceeds the set temperature by more than 25°C.
If either the "E1" or "E2" error appears, the device will automatically shut down.
Troubleshooting Steps:
- Immediately disconnect the power.
- Check surrounding and avoid direct airflow from AC units or fans, as they may affect heating.
- Allow the device to cool down, then restart it.
If the issue persists, contact our support with the error details for further assistance.
5.12 The heat plate doesn't rise
If the heat plate remains at the bottom, the mechanical structure may be stuck.
Troubleshooting Steps:
- Gently lift or adjust the heat plate manually to help it move. !!Be cautious of high temperatures to avoid burns.
- Press the "Start" button to reset the device while it is powered on
If the issue persists, contact our support with the error details for further assistance.
5.13 The heat plate doesn't descend
If the heat plate is not descending, try the following steps:
- Ensure the pull out drawer is fully pushed in all the way to the back of the machine.
- If the automatic mode is activated, the heat plate should automatically descend when the ironing board is pushed in.
- If the heat plate doesn’t descend automatically, press the "start" button after pushing in the board to activate it.
If the issue persists, contact our support with the error details for further assistance.
5.14 Why does the device beep/make weird noises?
The device may beep for several reasons:
-
One beep: This occurs when:
- The device reaches the set temperature.
- The countdown ends.
- The device auto-powers off.
- The pull out drawer is not fully pushed in.
- Beeps constantly with "E1" or "E2" on the screen: This indicates an error.
What to do:
- Immediately disconnect the power.
- Allow the device to cool down.
- Once cooled, restart the device.
If the issue keeps occuring please contact our support.
-
Noise from the heat plate:
- Occasional noise from thermal expansion and contraction during heating is normal and may decrease with use.
5.15 Why can't I adjust the pressure?
The LOKLiK Auto Heat Press allows adjustments for temperature and time only.
Tip:
If you need greater pressure, we recommend adding an extra heat press mat to achieve the desired effect.
5.16 Can't find your answer?
6 LOKLiK Auto Tumbler Heat Press
6.1 Where can I download the manual?
6.2 Why does the device emit slight smoke during or after heating?
It is normal for slight smoke to be emitted, as the sublimation ink sublimates into gas at high temperatures. This is a standard part of the sublimation process and should not be a cause for concern.
6.3 What is the time and temperature range of the LOKLiK Auto Tumbler Heat Press?
- Time: 1 - 600 seconds
- Temperature: 100°C - 200°C (210°F - 390°F)
6.4 How do I set the temperature unit (°C or °F) ?
Press the "Temp" button for 2 seconds to switch between temperature units (℃/℉).
6.5 Why do I get vague white spots in my results?
Please refer to the manual of the LOKLiK Auto Tumbler Heat Press for the correct settings. It's important to follow these settings to achieve the best results.
- White spots typically indicate that insufficient time or heat was applied during the pressing process.
- Ensure that the sublimation paper is wrapped tightly (but not so tight it bugles up) around the mug or tumbler you're pressing.
- Consider trying different mugs, sublimation paper, and ink of higher quality. For optimal results, we recommend
- using LOKLiK branded materials.
We recommend to use sublimation heat tape to ensure your design doesn't move.
6.6 Why are my image colors uneven or dull?
Please refer to the manual of the LOKLiK Auto Tumbler Heat Press for the correct settings. Following the recommended settings is essential for achieving the best results.
- Try increasing the temperature and/or pressing time to enhance color vibrancy. Some trial and error may be necessary to achieve the desired results*.
- Ensure that the sublimation paper is firmly attached to the tumbler using our LOKLiK sublimation heat tape to prevent shifting.
- Consider using different mugs, sublimation paper, and sublimation ink of higher quality.
For optimal results, we recommend using LOKLiK branded materials.
*For best results, we recommend using LOKLiK-branded materials, as different brands of mugs, tumblers, ink, or sublimation paper may affect the final outcome.
6.7 Why Are the Black Parts in My Results Brownish Instead of Black?
If the black areas of your design appear brownish, try the following solutions:
1. Check the Correct Settings
- Refer to the Impress Auto Tumbler manual for the correct temperature and time settings. Some trial and error may be necessary to achieve the desired results.
- Using the wrong settings can affect the final color quality.
2. Adjust Heat and Pressing Time
- A brownish tint usually indicates too much heat or pressing time.
- Try reducing the temperature and/or pressing time for better results.
3. Use High-Quality Materials
- The quality of your mugs, sublimation paper, and ink can impact the final outcome.
- For best results, we recommend using LOKLiK-branded materials, as different brands of mugs, tumblers, ink, or sublimation paper may affect the final outcome.
6.8 Why Does My Image Have a Double Shadow or Residue on the Tumbler?
If your image appears blurry or leaves residue, try these solutions:
1. Check the Correct Settings
- Refer to the Impress Auto Tumbler manual for the recommended temperature and time settings. Some trial and error may be necessary to achieve the desired results.
- Using incorrect settings can lead to ghosting or residue issues.
2. Adjust Heat and Pressing Time
- Try decreasing the temperature and/or pressing time to prevent overexposure, which can cause shadowing.
3. Secure the Sublimation Paper Properly
4. Use High-Quality Materials
- Low-quality mugs, sublimation paper, or ink can affect results.
- For best results, we recommend using LOKLiK-branded materials, as different brands of mugs, tumblers, ink, or sublimation paper may affect the final outcome
6.9 Why do my results have a paper texture?
- The ironing time may be too long. Try decreasing the pressing time to prevent the texture from transferring.
- Consider using different sublimation paper and ink of higher quality.
For optimal results, we recommend using LOKLiK branded materials.
6.10 Why does the sublimation paper look slightly yellow after pressing?
It is normal for sublimation paper to turn slightly yellow when exposed to high temperatures during the pressing process. This does not affect the final transfer result.
6.11 Can I press two mugs at the same time with the LOKLiK Auto Tumbler Heat Press?
We recommend pressing one mug at a time and to stay inside of the marked lines on the Auto Tumbler Heat Press for the best results. While it may be possible to press two mugs simultaneously, we cannot guarantee consistent or high-quality outcomes.
6.12 What size of mugs/tumblers can be pressed with the LOKLiK Auto Tumbler Heat Press?
- Diameter: 7.5 - 8.5 cm (2.9 - 3.3 inches)
- Length: Up to 21 cm (8.2 inches)
6.13 Can I use tumblers in any shape?
For the best transfer results, we recommend using straight tumblers.
With curved tumblers, the heat and pressure may not be distributed evenly across the surface, which could lead to poor or inconsistent results.
Using a straight tumbler ensures more uniform pressure and heat, resulting in a better and more reliable transfer.
6.14 Why does the error "E1" or "E2" appear on the screen?
- E1 with beep: This error occurs when the temperature hasn’t risen within 30 seconds during heating.
- E2 with beep: This error occurs when the temperature exceeds the set temperature by more than 25°C.
If either the "E1" or "E2" error appears, the device will automatically shut down.
Troubleshooting Steps:
- Immediately disconnect the power.
- Check surrounding and avoid direct airflow from AC units or fans, as they may affect heating.
- Allow the device to cool down, then restart it.
If the issue persists, contact our support with the error details for further assistance.
6.15 What if the heat is uneven or the transfer effect is poor?
Please refer to the manual of the LOKLiK Auto Heat Press for the correct settings. Following the recommended settings is essential for achieving the best results.
- Wait for the set temperature to be reached for the best ironing effect. Some trial and error may be necessary to achieve the desired results*
- Avoid using expired or low-quality materials. We recommend to use our LOKLiK materials.
- Before applying the material: Iron the fabric for 5-10 seconds first to remove moisture and wrinkles.
*For best results, we recommend using LOKLiK-branded materials, as different material brands and products may affect the final outcome.
6.16 Can't find your answer?
7 LOKLiK Easy Heat Press
7.1 Where can I download the manual?
7.2 Why does the device emit slight smoke during or after heating?
It is normal for slight smoke to be emitted, as the sublimation ink sublimates into gas at high temperatures. This is a standard part of the sublimation process and should not be a cause for concern.
7.3 What is the time and temperature range of the LOKLiK Easy Heat Press?
- Time: 1 - 600 seconds
- Temperature: 100°C - 210°C (210°F - 410°F)
7.4 How do I set the temperature unit (°C or °F) ?
Press the "Temp" button for 2 seconds to switch between temperature units (℃/℉).
7.5 What materials can be used with the LOKLiK Easy Heat Press?
The LOKLiK Easy Heat Press can work with a variety of materials, including:
If you're not sure if your material can be used, we recommend checking with the supplier to make sure it's safe.
7.6 What materials can the LOKLiK Easy Heat Press press on?
The LOKLiK Easy Heat Press is compatible with a variety of materials, including:
- Cotton
- Polyester
- Blends (Cotton-poly, etc.)
- And other fabrics, depending on the material and technique used for pressing.
Some third-party materials may work better than others, and the results can vary. We recommend contacting your supplier to confirm if it's compatible with our easy heat press and testing different settings to achieve the desired results.
7.7 The device won't turn on
- Ensure correct operation: After connecting the power, the power button will flash white. Press the power button once to turn on the device.
- Check voltage specification: Ensure that the device matches your area's voltage specifications.
If this didn't solve the issue please contact us.
7.8 Why does the error "E1" or "E2" appear on the screen?
- E1 with beep: This error occurs when the temperature hasn’t risen within 30 seconds during heating.
- E2 with beep: This error occurs when the temperature exceeds the set temperature by more than 25°C.
If either the "E1" or "E2" error appears, the device will automatically shut down.
Troubleshooting Steps:
- Immediately disconnect the power.
- Check surrounding and avoid direct airflow from AC units or fans, as they may affect heating.
- Allow the device to cool down, then restart it.
If the issue persists, contact our support with the error details for further assistance.
7.9 Why does the LOKLiK Easy Heat Press make beep sounds?
7.10 Why are the display numbers fluctuating?
- Normal screen behavior: It is normal for the displayed values to change, as the screen provides real-time recordings of time, temperature, pressure, and other metrics during operation.
- Unstable voltage: Fluctuations may occur due to unstable voltage. Ensure that the device matches your area's voltage specification. Check if the device is plugged in correctly.
7.11 Does the LOKLiK Easy Heat Press shut down automatically?
For safety, the LOKLiK Easy Heat Press automatically shuts down after 15 minutes of inactivity.
7.12 Can't find your answer?
8 LOKLiK ImPress™ Mini 3
8.1 Where can I download the manual?
8.2 Why does the device emit slight smoke during or after heating?
It is normal for slight smoke to be emitted, as the sublimation ink sublimates into gas at high temperatures. This is a standard part of the sublimation process and should not be a cause for concern.
8.3 What is the time and temperature range of the LOKLiK ImPress™ Mini 3?
- Time: 1 - 600 seconds (in steps of 5 sec.)
- Temperature: 100°C - 210°C (210°F - 410°F) (in steps of 5°C)
8.4 How do I set the temperature unit (°C or °F) ?
Press the "Set" button for 3 seconds to switch between temperature units (℃/℉).
8.5 Can I use the LOKLiK ImPress™ Mini 3 to press mugs, hats and curved surfaces?
Yes, the LOKLiK ImPress™ Mini 3 features a partially curved heat plate, allowing you to press on curved surfaces like mugs, tumblers, hats, and more.
8.6 What materials can be used with the LOKLiK ImPress™ Mini 3?
The LOKLiK ImPress™ Mini 3 can work with a variety of materials, including:
If you're not sure if your material can be used, we recommend checking with the supplier to make sure it's safe.
8.7 What materials can the LOKLiK ImPress™ Mini 3 press on?
The LOKLiK ImPress™ Mini 3 is compatible with a variety of materials, including:
- Cotton
- Polyester
- Blends (Cotton-poly, etc.)
- And other fabrics, depending on the material and technique used for pressing.
- Ceramic
- Glass
- Steel
- Sublimation coated surfaces
Some third-party materials may work better than others, and the results can vary. We recommend contacting your supplier to confirm if it's compatible with our LOKLiK ImPress™ Mini 3 and testing different settings to achieve the desired results.
8.8 How can I adjust the temperature?
To adjust the temperature, press the "Set" button once.
Then use the "+" and "-" buttons to increase or decrease the temperature.
8.9 How can I adjust the timer?
Press the "Set" button twice to enter the timer settings.
Then, use the "+" and "-" buttons to adjust the timer as needed.
8.10 Why does the LOKLiK ImPress™ Mini 3 make beep sounds?
8.11 Does the LOKLiK ImPress™ Mini 3 shut down automatically?
For safety, the LOKLiK ImPress™ Mini 3 automatically shuts down after 15 minutes of inactivity.
8.12 What if the heat is uneven or the transfer effect is poor?
- The LOKLiK Mini Heat Press is handheld, so pressure may vary during the process. If the transfer effect is uneven, try ironing again and applying more pressure.
- Wait for the set temperature to be reached for the best ironing effect.
- Avoid using expired or low-quality materials. We recommend to use our LOKLiK materials.
- Before applying the material: Iron the fabric for 5-10 seconds first to remove moisture and wrinkles.
- Make sure the correct time and temperature are set for the materials you're using.
- Ensure the heat plate fits the design properly.
8.13 What to do when the device stops working suddenly?
- Ensure the device is powered on.
- Turn off the power by pressing the 'start' button or unplugging the power cable, then restart the device.
If the issue persists, contact our support with the error details for further assistance.
8.14 The buttons don't react
- Ensure the device is powered on.
- Turn off the power by pressing the 'start' button or unplugging the power cable, then restart the device.
If the issue persists, contact our support with the error details for further assistance.
8.15 What’s the size of the heat plate?
The LOKLiK ImPress™ Mini 3 has a heat plate size of 9.3 × 8 cm.
8.16 How to work with the curved heat plate?
The LOKLiK ImPress™ Mini 3 is designed for curved surfaces like cups, hats, and shoe heels. Ensure firm, even pressure while ironing to achieve the best transfer results.
8.17 How to sublimate a cup successfully with the curved heat plate?
- Read the quick reference chart carefully before starting.
- Ensure the cup's diameter is between 7.6 cm and 8.2 cm for the best results.
- Make sure the curved heat plate fits perfectly over the design when ironing.
- Use high-quality sublimation cups for optimal transfer results (recommended brand: LOKLiK).
8.18 How to get a successful heat transfer result?
Ensure the time and temperature settings are suitable for the materials you're using.
Make sure the heat plate fits the design perfectly to achieve an even transfer.
8.19 What can the insulated safety base be used for?
- Store the heat press when not in use.
- Use the base as a cup holder when sublimating cups.
8.20 How to convert the temp unit?
Press the "Set" key for 3 seconds to convert the temperature unit (°C/°F).
8.21 Can't find your answer?
9 LOKLiK Mini Heat Press
9.1 Where can I download the manual?
9.2 Why does the device emit slight smoke during or after heating?
It is normal for slight smoke to be emitted, as the sublimation ink sublimates into gas at high temperatures. This is a standard part of the sublimation process and should not be a cause for concern.
9.3 What is the temperature range of the LOKLiK Mini Heat Press?
The LOKLiK Mini Heat Press has 3 temperature settings:
- 1 indicator light: 140°C / 284°F
- 2 indicator lights: 160°C / 320°F
- 3 indicator lights: 180°C / 356°F
9.4 What materials can be used with the LOKLiK Mini Heat Press?
The LOKLiK Mini Heat Press can work with a variety of materials, including:
If you're not sure if your material can be used, we recommend checking with the supplier to make sure it's safe.
9.5 What materials can the LOKLiK Mini Heat Press press on?
The LOKLiK Mini Heat Press is compatible with a variety of materials, including:
- Cotton
- Polyester
- Blends (Cotton-poly, etc.)
- And other fabrics, depending on the material and technique used for pressing.
Some third-party materials may work better than others, and the results can vary. We recommend contacting your supplier to confirm if it's compatible with our easy heat press and testing different settings to achieve the desired results.
9.6 How can I adjust the temperature on the LOKLiK Mini Heat Press?
The LOKLiK Mini Heat Press uses a single button for temperature control. To adjust the temperature:
- Press the button to cycle through the settings.
- The button logic is as follows: On → Low → Medium → High → Off.
- Adjust to your desired setting accordingly.
The LOKLiK Mini Heat Press has 3 temperature settings:
- 1 indicator light: 140°C / 284°F
- 2 indicator lights: 160°C / 320°F
- 3 indicator lights: 180°C / 356°F
9.7 Why does the LOKLiK Mini Heat Press make beep sounds?
- Beeps with the 4 indicator lights flashing red: Error: No heating increase, it means the temperature hasn’t risen within 5 seconds.
The device will shut down automatically.
Let the device cool down and restart it.
- beeps with the 4 indicator lights flashing green: Error: Overheating, it means the device has exceeded the set temperature by more than 5°C.
The device will shut down automatically.
Let the device cool down and restart it.
If the issue keeps occuring please contact our support.
9.8 Does the LOKLiK Mini Heat Press shut down automatically?
For safety, the LOKLiK Mini Heat Press automatically shuts down after 10 minutes of inactivity.
9.9 What if the heat is uneven or the transfer effect is poor?
- The LOKLiK Mini Heat Press is handheld, so pressure may vary during the process. If the transfer effect is uneven, try ironing again and applying more pressure.
- Wait for the set temperature to be reached for the best ironing effect.
- Avoid using expired or low-quality materials. We recommend to use our LOKLiK materials.
- Before applying the material: Iron the fabric for 5-10 seconds first to remove moisture and wrinkles.
9.10 How can I know the LOKLiK Mini Heat Press has reached the maximum temperature?
When the set temperature indicator lights turn from red to green.
The LOKLiK Mini Heat Press has reached the set temperature:
- 1 indicator light: 140°C / 284°F
- 2 indicator lights: 160°C / 320°F
- 3 indicator lights: 180°C / 356°F
9.11 What’s the size of the heat plate?
The LOKLiK Mini Heat Press has:
- A heat plate size of 6.6 x 11 cm
- Machine dimensions of 23 x 13 x 8 cm
- Weight of 0.62 kg
9.12 Can't find your answer?
10 LOKLiK ImPress™ Hat
10.1 Where can I download the manual?
10.2 The buttons don't react
- Ensure the device is powered on.
- Turn off the power by pressing the 'start' button or unplugging the power cable, then restart the device.
If the issue persists, contact our support with the error details for further assistance.
10.3 What is the temperature range of the LOKLiK ImPress™ Hat?
- Time: 1 - 600 seconds
- Temperature: 100°C - 200°C (210°F - 390°F)
10.4 How do I set the temperature unit (°C or °F) ?
Press the "Set" button for 3 seconds to switch between temperature units (℃/℉).
10.5 Why does the LOKLiK ImPress™ Hat make beep sounds?
10.6 What to do when the device stops working suddenly?
- Ensure the device is powered on.
- Turn off the power by pressing the 'start' button or unplugging the power cable, then restart the device.
If the issue persists, contact our support with the error details for further assistance.
10.7 Why does the error "E1" or "E2" appear on the screen?
- E1 with beep: This error occurs when the temperature hasn’t risen within 30 seconds during heating.
- E2 with beep: This error occurs when the temperature exceeds the set temperature by more than 25°C.
If either the "E1" or "E2" error appears, the device will automatically shut down.
Troubleshooting Steps:
- Immediately disconnect the power.
- Check surrounding and avoid direct airflow from AC units or fans, as they may affect heating.
- Allow the device to cool down, then restart it.
If the issue persists, contact our support with the error details for further assistance.
10.8 Why doesn't the hat fit tightly to the ironing mat?
- Place the hat vertically with the brim facing upward on the ironing mat.
- Release the hat buckle and adjust accordingly to ensure a secure fit.
10.9 How to ensure successful transfer results?
- Make sure the time and temperature settings are suitable for the materials you're using.
- Ensure the hat is perfectly fit to the ironing mat.
- Securely fix the design to the hat.
- Cold peel off the protective film after pressing.
- Avoid using expired or poor-quality materials. Recommended brand: LOKLiK.
10.10 How do you fix the design on the hat?
Use heat-resistant tape to secure the design to the hat before ironing.
10.11 Why does the device emit slight smoke during or after heating?
It is normal for slight smoke to be emitted, as the sublimation ink sublimates into gas at high temperatures. This is a standard part of the sublimation process and should not be a cause for concern.
10.12 Can't find your answer?
11 Other questions
11.1 Which payment methods can I use?
You can view all available payment options during the checkout process.
Please note that payment methods may vary depending on your device, country or region. Not all options may be available in every location.
We generally offer the following payment methods:
- Credit card
- Debit card
- Bank transfer
- PayPal
- PayPal Pay Later (conditional on PayPal’s approval)
- Klarna
- Google Pay
- Apple Pay
For more information about a payment method, you can visit their website or contact your bank.
When a payment method offers the option to buy on credit or in installments, this is conditional on the payment provider's credit approval.
LOKLiK Europe does not have any control over the credit approval process. Any questions about this should be directed to the payment method in question.
12 Can't find your answer?
12.1 Contact our support